A Comprehensive Overview to the Plastic Shot Molding Modern Technology
Plastic injection molding stands as a foundation of modern manufacturing, providing unparalleled efficiency and accuracy in the manufacturing of complicated plastic parts. As the landscape of producing advances, understanding the future trajectory of shot molding becomes significantly necessary.

Overview of Plastic Shot Molding
Plastic shot molding is a commonly used production process that allows the reliable manufacturing of complex plastic get rid of high precision. This innovation has come to be a foundation in different sectors, consisting of automobile, durable goods, and electronic devices, owing to its ability to generate large amounts of parts quickly and cost-effectively.
The procedure includes melting plastic granules and injecting the molten product into a pre-designed mold. When cooled down, the mold is gotten rid of to expose the ended up element, defined by its complex details and uniformity. The convenience of products made use of in plastic shot molding, varying from thermoplastics to thermosetting polymers, permits makers to tailor items to satisfy specific demands, such as flexibility, resistance, and stamina to warmth or chemicals.
Moreover, the efficiency of this technique lowers waste and lessens production prices, making it an eye-catching alternative for services aiming to optimize their manufacturing processes. As technology developments, advancements such as multi-material injection molding and the integration of automation remain to improve the capacities of plastic shot molding, enabling the development of progressively innovative items that satisfy the demands of modern markets.
The Injection Molding Refine
Shot molding is an advanced manufacturing strategy that involves several essential steps to transform raw plastic materials right into ended up products. The procedure begins with the preparation of plastic pellets, which are fed right into a heated barrel. Here, the pellets are melted and homogenized to achieve an uniform thickness.
As soon as appropriately warmed, the molten plastic is infused into a precisely engineered mold under high stress. This action is crucial, as it allows the material to load every dental caries of the mold, making sure the last product properly mirrors the desired design. The injection time should be meticulously managed to avoid issues and make certain efficient product usage.
After the mold is filled, it undergoes a cooling stage, where the plastic solidifies into its final form. This cooling procedure can vary in period relying on the thickness and complexity of the part. Once cooled, the mold opens up, and the completed product is expelled.
Trick Benefits of This Modern Technology
Among the most significant benefits of shot molding technology depends on its capacity to create high quantities of accurate and constant parts with very little waste. This efficiency comes from the automatic nature of the process, which substantially decreases manual work and the potential for human error. Therefore, suppliers can attain a high level of repeatability in their outcome, ensuring that each component meets stringent top quality requirements.
Another secret benefit is the flexibility of products that can be used in injection molding. A broad variety of thermoplastics and thermosetting polymers can be built, permitting customized residential or commercial properties to suit certain applications. The modern technology supports intricate geometries and intricate layouts, which can be testing to accomplish with various other manufacturing methods.
The preliminary financial investment in molds may be high, yet the lasting savings in material waste and labor make shot molding a financially sensible option. These benefits solidify shot molding's position as a recommended production process across different industries - Plastic Injection Molding.
Applications Throughout Industries
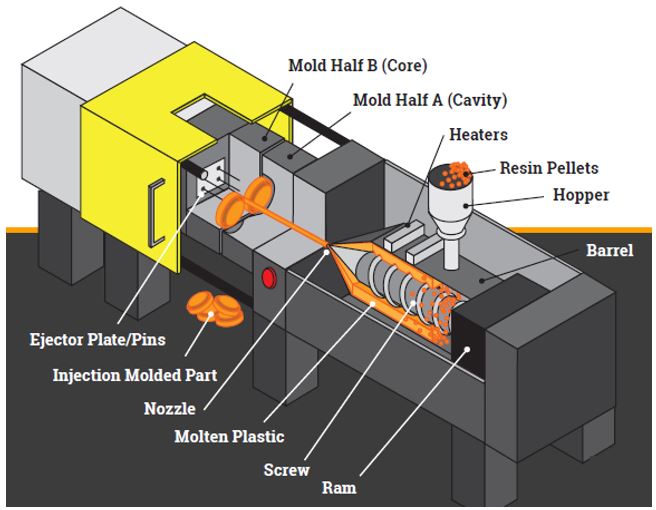
In the clinical area, injection molding is essential for producing high-quality, sterile parts, consisting of syringes, surgical instruments, and housings for medical gadgets. The capability to keep limited resistances and generate intricate geometries makes it a perfect choice for these applications. Furthermore, the packaging market advantages from injection molding by creating a vast array of containers, closures, and dispensers pop over here that are both economical and reliable.
The plaything market depends greatly on injection molding to produce vibrant, resilient, and safe items that interest youngsters. The building and construction sector makes use of injection molding for creating numerous fixtures, fittings, and elements that contribute to both performance and layout. On the whole, the wide selection of applications shows the click this link important role of injection molding technology in advancing different sectors.
Future Patterns in Shot Molding
Accepting developments in technology, the future of shot molding is poised for significant improvement driven by innovations in materials, automation, and sustainable methods. One of the most notable trends is the growth of bio-based and recycled polymers, which not only decrease reliance on fossil fuels yet likewise minimize environmental effect. As makers increasingly prioritize eco-friendly options, these products are coming to be more widespread in production.
Automation is one more crucial pattern shaping the navigate here sector. The combination of robotics and artificial intelligence into the injection molding procedure boosts accuracy, performance, and manufacturing speed. Smart factories furnished with IoT devices permit real-time tracking and anticipating upkeep, lowering downtime and enhancing operational procedures.
Additionally, the shift towards personalized and small-batch production is obtaining energy. Advanced modern technologies such as 3D printing and additive manufacturing make it possible for fast prototyping and the creation of complex geometries that were formerly unattainable. This change enables business to respond better to market demands and consumer preferences.
Conclusion
In conclusion, plastic injection molding innovation represents a foundation of modern-day manufacturing, providing effectiveness and convenience in producing complex parts throughout diverse sectors. The in-depth evaluation of the injection molding procedure highlights its critical phases and advantages, while the expedition of applications underscores its prevalent significance.
Plastic shot molding stands as a foundation of modern production, supplying unequaled efficiency and accuracy in the production of facility plastic components (Plastic Injection Molding). The versatility of products used in plastic injection molding, ranging from thermoplastics to thermosetting polymers, permits suppliers to tailor products to fulfill particular requirements, such as adaptability, resistance, and stamina to warmth or chemicals
Shot molding is an innovative manufacturing method that involves several important steps to transform raw plastic materials into completed items.The versatility and effectiveness of shot molding innovation have actually led to its extensive fostering across numerous industries.In final thought, plastic injection molding technology represents a foundation of modern-day manufacturing, supplying effectiveness and convenience in generating intricate parts across diverse sectors.